多层PCB板在压合过程中的常见问题原因
发表时间:2022-10-08 09:00:03 人气:6354
伴随着科技的不断发展,单双面板已经不能满足部分市场的需求,多层板得到了很大的发展,PCB厂多层板的制作必须要经过压合这一个步骤,压合是利用高温高压使半固化片受热融化,并使其流动,再转化为固化片。从而将一块或者多块内层蚀刻后板(经黑化或者棕化处理)以及铜箔粘合成一块多层板的制程。该制程还包括将压合前的排版,压合后的多层板进行钻定位孔及外形加工。而在此过程中也会遇到很多问题,下面我们来介绍一下可能遇到的问题及发生原因。
一、厚薄不均,内层打滑
1、同一窗口的成型板总厚度不同;
2、印制板在成型板的累积厚度偏差大;热压模板的平行度差,层压板可以自由位移,整个叠层又偏向热压模板的中心。
二、板面有凹坑、树脂、褶皱
1、LAY-UP操作不当,钢板表面未干燥有水渍,造成铜箔起皱;
2.压板时,板面失压,造成树脂流失过多,铜箔下胶不足,铜箔表面起皱。
三、内层图案移位
1、内层图案铜箔剥离强度低或耐温性差或线宽过细;
2、预压过高,树脂的动态粘度小;
3.按压模板不平行。
四、层间错位
1、内层材料的热膨胀、胶粘片的树脂流动;
2、贴合时的热收缩;
3、层压材料与模板的热膨胀系数差别很大。
五、 发泡
1、预压过低;
2、温度过高,预压与全压间隔时间过长;
3、树脂的动态粘度高,全压施时间晚;
4、挥发物含量高;
5、粘合面不干净;
6、活动性差或预压不足;
7、板子温度低。
六、板材翘曲、板材翘曲
1、不对称结构;
2、固化周期不足;
3、粘合片或内覆铜板的下料方向不一致;
4、板内采用不同厂家的多层板或胶板。
5、多层板固化施压后处理不当。
七、分层、热分层
1、内层湿度大或挥发成分高;
2、胶纸挥发成分高;
3、内层表面污染;异物污染;
4、氧化层表面呈碱性;表面有亚氯酸盐残留物;
5、氧化异常,氧化层结晶过长;预处理没有形成足够的表面积。
6、钝化效果不够。
八、白色外露玻璃布质纹路
1、树脂流动量过高;
2、预压过高;
3、施加高压的时机不对;
4、胶粘片的树脂含量低,凝胶时间长,流动性强。
以上就是关于PCB多层板在压合过程中常见问题原因,成都子程电子设备有限公司专注PCB行业13年,关注我们获得更多行业知识。
相关咨询
工厂展示
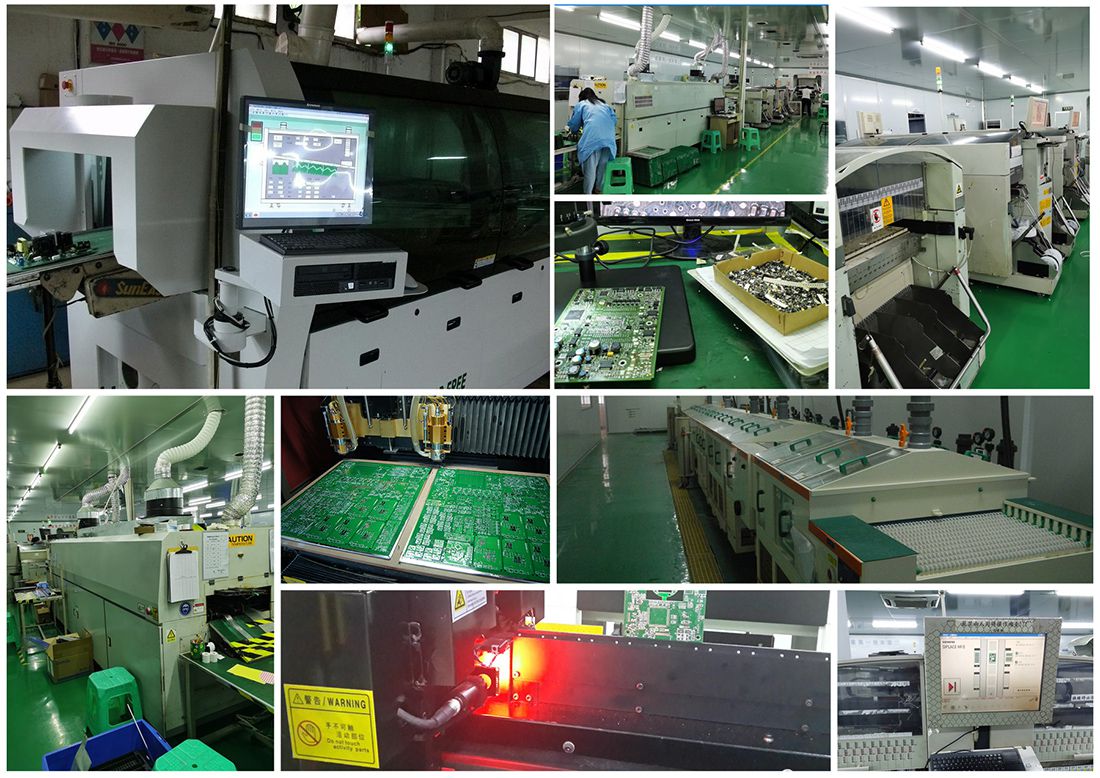
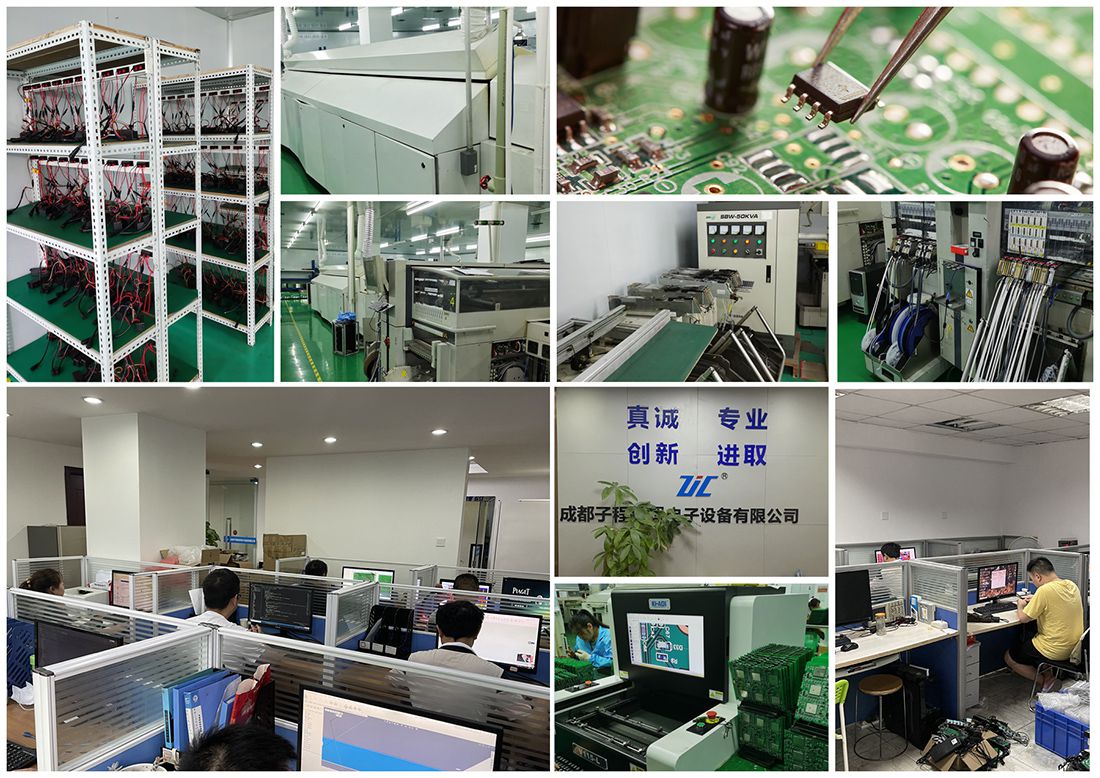
联系我们
成都子程新辉电子设备有限公司
联系人:文先生
手机:13183865499
QQ:1977780637
地址:成都市金牛区星辉西路2号附1号(台谊民生大厦)407号
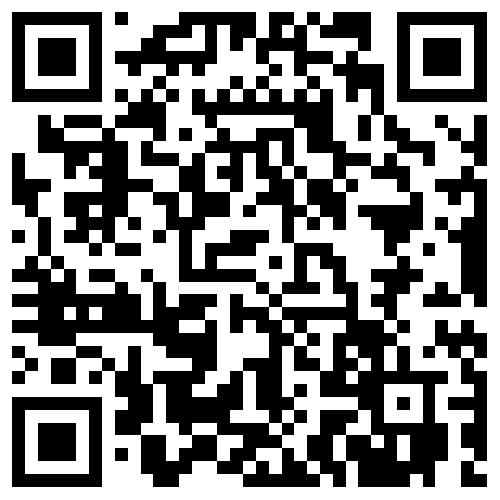